Field/Onsite Calibration Services
Save time with onsite support
Our onsite coordination services are fully customizable to meet your company’s specific equipment needs. Our site coordination services include:
- Regular internal calibration audits against ISO 9001, AS9100, ISO 13485 and many other international quality standards
- Complete database administration (including document management)
- New equipment set-up into your quality controlled system
- Equipment status management (active, inactive, reference only), with contact and location management
- Departmental or individual-level equipment recall
- Management of multiple calibration vendors
- Free ISO-compliant data entry to your online database
You select the responsibilities you wish to outsource from a list we design specifically for your company. This process guarantees a calibration measurement and maintenance program that works for you.
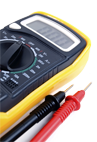
“Using usCalibration was such a good decision. We were having problems getting our last vendor to send certificates. usCalibration comes in with laptops and prints the certificates for us to have before they leave.”
– Rick Eaton, Director of Quality, AAA Plating
Read More
To set up an onsite visit, please follow these steps:
- Assure an accurate list of items to be physically available when our technician is present.
- Send us the list of instruments to be calibrated and a PO or PO number. A confirmed list that includes all the calibration information (Identification numbers, models, descriptions, calibration intervals, etc.) and your purchase documentation are required to ensure that you receive the correct service. If accredited calibration is needed, please specify “ISO/IEC 17025:2017 Accredited Calibration” on your purchase order.
- Schedule our Field Engineers to visit your company. Contact our sales representatives at 949-724-9474 x223 to make arrangements. We have a team of engineers ready to meet your technical and logistical needs.
- Prepare for the visit. Coordinate the readiness of equipment to be calibrated with the instrument users and prepare a workspace for our engineers’ use during our visit. Each engineer needs a work area that is approximately 3’x6’ with an available electrical outlet.
During your onsite visit please follow these steps to ensure a steady workflow and to avoid any unnecessary idle time and associated costs:
- Have a point person designated to meet the Field Engineers at the scheduled start time and to maintain a steady supply of instruments for the engineers to calibrate.
- Have all equipment ready and identified when the Field Engineers arrive. Be specific as to where the equipment is located.
- Moveable equipment (hand tools, handheld and bench-top meters and test equipment, etc.) should be placed in a clear location waiting for the engineers to calibrate.
- Equipment that is not practical to move (panel meters, temperature controllers, etc.) should be marked or tagged when practical and their location should be specifically shown to the engineers when they arrive.
- Unlock any locked equipment to provide easy access for the Field Engineer.
- Inform the engineers of any plumbing, assembly or disassembly requirements for the equipment.
- Inform the Field Engineers of any additional equipment to be calibrated or any changes to calibration information (ID #’s Serial #’s, Model #’s, Manufacturer, Calibration Interval, Descriptions, etc.) prior to the start of any work.
Need your equipment calibrated now? usCalibration offers same-day, next-day, and various expedite options to meet all your calibration needs. Turn to usCalibration for your one-stop-calibration-shop and get back to focusing on what you do best. Learn more.